超凡效能Romax软件畅享智能设计巅峰新视界
19429202025-03-25下载地址27 浏览
1. 传统设计工具为何被智能平台取代?
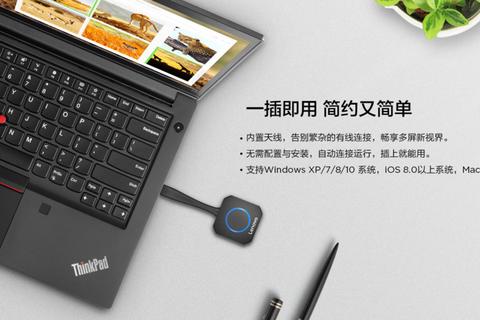
在机械传动领域,工程师曾长期面临一个矛盾:如何平衡设计精度与开发效率?传统设计工具往往采用“分步式”分析,齿轮、轴承、轴等部件需单独建模,导致系统级耦合效应被忽视,最终引发样机测试失败率高、开发周期冗长等问题。例如,某风电企业曾因齿轮箱行星轮系载荷分配不均导致批量故障,仅样机修改成本就超千万元。
而超凡效能Romax软件畅享智能设计巅峰新视界通过参数化建模与系统级仿真,彻底改变了这一局面。以3兆瓦风电齿轮箱为例,RomaxDesigner可在同一平台完成行星轮系、轴承刚度与轴变形的耦合分析,精准预测载荷分配误差范围小于5%,并通过德国GL认证。这种“从零件到系统”的一体化设计模式,使开发周期从18个月缩短至10个月,效率提升44%。
2. 柔性耦合分析如何破解行业痛点?
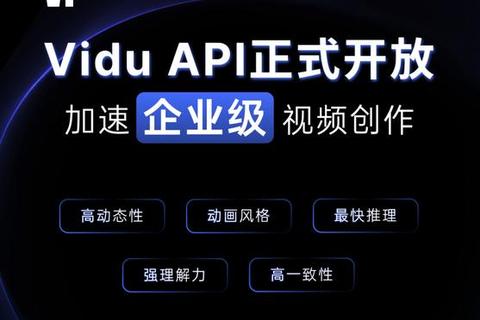
机械传动系统的复杂性在于:微小部件变形可能引发连锁反应。例如,汽车变速箱中轴承预紧力的细微偏差,会导致齿轮错位磨损,进而影响整车NVH性能。传统方法因缺乏多物理场耦合工具,常采用“经验值+冗余设计”的保守策略,造成材料浪费与成本上升。
超凡效能Romax软件畅享智能设计巅峰新视界的“柔性耦合分析”功能,正是针对这一痛点的革新。其核心在于:
轴承非线性建模:支持球轴承、圆锥滚子轴承等9类滚动轴承的刚度随载荷变化特性,预紧力优化误差低于3%;
齿轮错位补偿:通过平行轴建模器计算多级齿轮箱变形量,自动生成齿面修形方案,使啮合错位容差提升30%;
动态载荷谱叠加:可同时加载转速波动、扭矩冲击等复杂工况,为齿轮疲劳寿命预测提供高达95%置信度的数据支撑。
某新能源汽车企业采用该软件后,变速箱轴承寿命预测准确率从78%提升至92%,材料成本降低17%。
3. 智能设计如何赋能跨行业创新?
从风电齿轮箱到航空航天传动系统,超凡效能Romax软件畅享智能设计巅峰新视界展现了强大的行业适配性:
风电领域:针对3兆瓦以上大功率机型,其行星轴建模器2(S04-2)可处理复合式行星轮系,支持辛普生式(Simpson)和拉威挪式结构优化,帮助大连重工•起重集团实现齿轮箱功率密度提升21%;
汽车工业:多速比变速器建模器(S03-2)支持离合器状态切换与多载荷谱分析,使某车企手动变速器换挡力波动范围从±15N压缩至±5N;
航天特种传动:通过动力学模块的模态振型分析,某卫星太阳翼驱动机构谐振风险降低90%,设计迭代次数减少60%。
这些案例印证了其“平台化工具+行业知识库”模式的优越性——既提供标准化分析模块,又内置FAG、SKF等轴承数据库及材料工程库,降低80%的基础数据录入工作量。
未来设计者的行动指南
对于企业而言,引入超凡效能Romax软件畅享智能设计巅峰新视界需分三步走:
1. 需求匹配:优先启用基础模块(S02-1)进行单轴系统验证,再逐步扩展至行星齿轮、多速比变速器等高级模块;
2. 数据沉淀:建立企业专属的轴承参数库与材料性能库,与RomaxWIND认证报告体系对接,加速GL、ISO等国际认证流程;
3. 人才迭代:结合软件自带的HTML格式分析报告与BMP/WMF可视化工具,构建“仿真-测试-优化”闭环能力。
正如某工程师在PET瓶生产线改造项目中的评价:“过去需要3次样机迭代才能解决的问题,现在通过Romax的虚拟验证一次成功。”这或许正是智能设计时代最值得期待的新视界。